1. Introduction
The HACCP Transport guideline is intended to support GMP+ FSA certified companies (or companies who wish to become GMP+ FSA certified) in setting up their in-company HACCP systems. The guideline provides an interactive example of an HACCP plan and has been developed with Quality Managers and Auditors with expertise in the field of Road Transport based in different Countries.
This guideline aims to provide support in feed and food safety assurance, for the management and employees of companies with the scope “Road transport of feed” in developing a company-specific HACCP system. The manner in which HACCP is described in the GMP+ FC scheme 2020 and document S9.4 Applying HACCP assessmentserved as a guideline in preparing this HACCP tool. See S9.4 for more information about HACCP.
For definitions and terminology, please check F0.2 Definition list.
Helpful tip
This symbol signifies supplementary and specific attention for the relevant issue
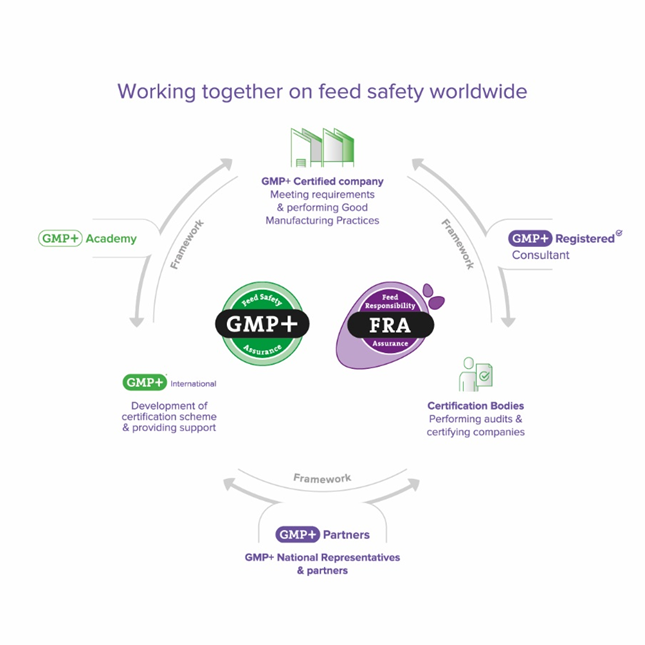
By choosing the GMP+ Feed Certification scheme, you are choosing to work together with the GMP+ Community to add value to your products and company. This ensures safe and responsible feed –and therefore safe food – for everyone all over the world.
1.1. Scope of this document
This document applies to (GMP+ certified) companies with the scope “Road transport of feed”, irrespective of their type or size, responsible for one or more of the following roles:
- ordering the transport of bulk and/or packaged feed;
- arranging the transport of bulk and/or packaged feed;
- the physical transport of bulk and/or packaged feed.
It is not important whether these roles are performed on own account or as (sub)contractors (‘service providers’). For each role, the company is obliged to develop and implement a HACCP plan.
GMP+ International supports you with an interactive example HACCP plan (Excel file). This HACCP plan includes the following activities:
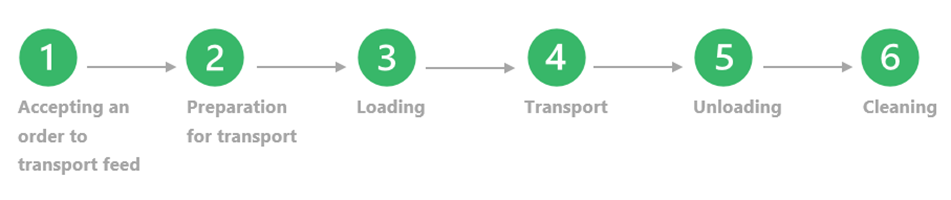
Keep in mind that other risks related to (feed and non-feed) activities which are not covered under the scope of GMP+ certification must also be controlled. These activities can have a negative impact on feed safety and for this reason control measures, based on an HACCP analysis, must be implemented and monitored to assure them. All these activities must be available for inspection/auditing.
1.2. HACCP Transport within the GMP+ FC scheme
Each transport company must identify, analyse and control the company-specific feed safety hazards by applying HACCP principles as stated in R1.0. This document describes the most common risks and associated control measures related to the different activities within the scope “Road transport of feed”. This means that in the event that other risks occur – in the company-specific situation – they must also be controlled by means of control measures. These control measures can be part of a prerequisites programme, or the company may implement them as specific measures for controlling a particular Critical Control Point.
It is emphasized that – in the end – every GMP+ certified company is responsible for its own correct and complete implementation of the GMP+ feed safety management system – including the HACCP plan – and is required to demonstrate this in the context of the certification. The information in this document is exclusively intended for illustrative purposes and as a tool to make a company’s own HACCP plan. GMP+ International can in no way be held liable for the use of the information provided.
2. How to make a company-specific HACCP plan – work instruction
Carrying out a HACCP assessment is the obligation and responsibility of the certified company itself. GMP+ provides support in the form of this tool and the auditor checks for conformance.
The GMP+ FC scheme is a chain system. Each link in the chain must guarantee the safety of feed (products) on the basis of the same principles as expressed in (product) norms. The basic principle for every transport company is that the products are transported in such a way that risks are controlled and the products are handled with the same safety levels before loading, during transport and at the moment of delivery.
HACCP is the tool to obtain insights into the risks during these steps and how to control them. The circumstances of each type of transport are different. This means that this generic HACCP assessment cannot be used simply as it is. Adaptation to the specific circumstances of the individual transport company is needed. For this reason, the tool is interactive. By implementing the following steps, you can make your company-specific HACCP plan. The totality of information is then a summary of your HACCP plan.
Start here:
Step 1: Compare activities and risks with the situation at your company
For each process step, assess per activity (Column B) whether the risks in Column C are applicable to your company or not.
- If a hazard (column C) is applicable, continue with step 2
- If a hazard (column C) is not applicable, you can delete the entire row.
- If activities are missing, create an extra row. Add to this row the missing activity (column B) and the related information in columns C, D and E. Continue with step 2
Helpful tip
Customer requirements play a significant part in the process step "Accepting an order to transport feed (contract acceptance)". Don't forget to include the possible risks related to customer requirements in the table.
Step 2: Determine the risk category (column H)
To determine the risk category, you need to follow the next steps. Depending on the outcome of the risk category, actions may be needed (see 2.3).
2.1 Define the likely occurrence (column F) for each hazard
For each applicable hazard, you need to select how likely they are to occur.
The likely occurrence is determined by the company-specific circumstances. Therefore, you must determine the likely occurrence yourself. By default, the likely occurrences are is always set to medium in the Excel file. Via a dropdown menu, you can select the applicable Likely occurrence : Low, Medium or High.
Likely occurrence | E xplanation |
Low | theoretically possible but hardly occurs in practice |
Medium | may occur, has been known to occur with some frequency |
High | occurs frequently |
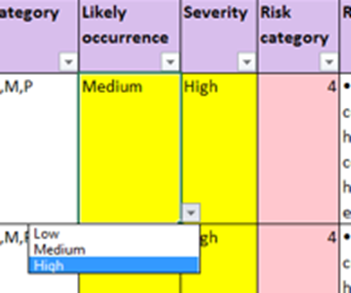
2.2 Define the Severity (column G) for each hazard
A recommendation for the severity level is given in column G. You have the option of deviating from this level. You can select the applicable severity via a dropdown menu. This deviation needs to be justified.
2.3 Determine Risk Category
By default, all the Risk Categories are set to 3 in the Excel file. Depending on the selected likely occurrence and severity, the risk category will be generated automatically:
| Likely occurrence | |||
Low | Medium | High | ||
S e v erity | High | 3 | 4 | 4 |
Medium | 2 | 3 | 4 | |
Low | 1 | 2 | 3 |
Risk Category 1 or 2
Risks falling into in risk categories 1 or 2 (see column H in the table) are general risks which can be controlled via a prerequisite programme. A minimum level of feed safety control must have been achieved before implementing HACCP. This minimum level is also applicable to transport activities, irrespective of their type or size. The prerequisite programme consists mainly of general control measures. These include pest control plans, cleaning and sanitising plans, training plans, maintenance plans, purchasing procedures and complaints handling. The prerequisite programme is part of the GMP+ FSA module, R1.0paragraph 8.2 and TS 1.1 Prerequisite Programme (PRP).
These general control measures are listed in Column J and form a basis for effective application of the hazard analysis for each transport company. In some cases, additional control measures are needed. These control measures are also given in column J.
You must determine whether the proposed control measure(s) provide an adequate basis for successful application of the HACCP plan. If this is not the case, you must specify and implement other (additional) control measures to control the risk.
For each control measure, you must specify the following information:
- Responsible person for the control measure*
- Evidence of the control measure**
* Responsible person
Add a responsible person for each control measure (column K). This is linked to a role (e.g. Manager, Quality Manager, Driver, Planner). Depending on the size of the company, different roles may be divided between different people, while within smaller companies one person may have several roles. Where this is the case, it may be easier to add the name of the responsible person.
** Evidence of Control measure
Add the applicable evidence in column L
Note: A control measure is an action to prevent the risk (as stated in column H) e.g. a phone call. Keep in mind that you need to be able to prove that you have carried out the control measure.
Risk Category 3 and 4
In the event that "severity X likely occurrence" results in risk category '3 or 4', specific (additional) control measure(s) are needed to control the risk. Suggestions for specific control measures are listed in the table, column J. Check if these suggestions fit your company specific situation and select the applicable control measures.
If the control measures do not fit, come up with a specific control measure(s) that is suitable for your company, with the aim of controlling the risk (as shown in column H) and state this control measure in column J.
Continue with step 3. You need to consider in advance what corrective action is needed if the hazard situation (as stated in column C) does occur.
Step 3: Complete your company-specific HACCP plan
The risks resulting in risk category 3 and 4 need to be controlled and therefore monitoring with a certain frequency is needed. If the risk is not under control, the safety of the product being transported can no longer be assured. For this reason, you must establish corrective action(s) to prevent a potentially unsafe product from entering the feed chain.
For all the risks resulting in risk category 3 and 4, you must provide the following information per risk:
- How to monitor
- Frequency of monitoring
- Correction, which must be carried out in case the hazard does occur*
- Responsible person for this correction**
- Evidence of correction***
*Corrections
Corrections are actions to eliminate a detected nonconformity. A correction may be, for example:
- In the event of contact with a prohibited load: reject the order
- In the event of loading the wrong product: stop loading,
- In the event of (possible) contamination of the loading compartment: refuse the trailer and clean the loading compartment with the aim of achieving a loading compartment which is clean, free of residues or odour.
In all these examples, always inform the customer and together decide which follow-up action is needed.
** Responsible person
Add a responsible person for each correction (column P). This is linked to a role (e.g. Manager, Quality Manager, Driver, Planner). Depending of the size of the company, different roles may be divided between different people, while within smaller companies one person may have several roles. Where this is the case, it may be easier to add the name of the responsible person.
*** Evidence for correction
Add the applicable evidence for the correction in column Q.
Note: A correction is an action to eliminate the risk, e.g. a phone call. Keep in mind that you need to be able to prove that you have carried out the correction.
In case a correction is needed, immediately assess whether the process and control measures (as stated in column J) need to be improved with the aim of preventing the risk from happening again. All the corrections need to be reviewed at least annually (R1.0paragraph 8.6.2.2. and 9.3.).
Step 4: Update the HACCP plan
The totality of information from steps 1-3 is a summary of your HACCP plan. This HACCP plan needs to be updated. This means that a review is needed at least once per year and immediately after new relevant information is available. This includes when:
- Roles within your company change (see 1.1)
- There are changes in the activities of your company
- Corrections are needed
- The IDTF database is updated with new products or cleaning regimes
See R1.0 paragraph 10.3. for the specific requirements on updates to the HACCP plan.
Helpful tip
- Be critical and create an open culture: personnel must feel free to report mistakes so that the company can take necessary control measures (e.g. training). Train personnel to signal and report issues.
- You can use complaints to measure the effectiveness of the control measures.
Risk Management tools
Where to find more about the Risk Management tools? Fact sheets More information: GMP+ Platform Product list More information: Product List Risk Assessments More information: GMP+ Platform GMP+ Monitoring database More information: GMP+ Monitoring database Support documents More information: Support documents |