1. Introduction
According to R 1.0 § 8.7.2.4, the certified company must have a documented procedure that demonstrates that the certified company is able to ensure the timely withdrawal/recall of products that have been identified as unsafe. This document supports the GMP+ certified company in establishing a recall procedure.
2. Contents of the Recall procedure
A recall procedure can contain the following components:
- Foreword by the general manager
- Flow chart of a recall action
- Reasons for a recall action
- Responsibilities and authorities of the recall coordinator and the recall team
- Criteria for starting and ending a recall
- Planning and establishing procedures for an effective and fast recall action
- Emergency measures
- Information for employees
- External information, customers, parties in the chain,), certification bodies, branch organisations, competent authority, media, other persons concerned
- Sample texts for press releases, advertisements, warnings, letters
- Follow-up lists, lists of contact persons, media lists, lists of external experts
- Registration of data and experiences
- Reporting and evaluation
- After-care
The nature and size of a recall procedure depends on the size and complexity of the company. The following paragraphs will describe the different components of a recall plan.
2.1. Forward
In the foreword the general manager indicates that a recall action takes precedence over all other organisation activities and that in a recall action all possible organisational resources are available to the recall team. A recall is important for the reduction of consequential damage to the certified company and its customers as well as to retain trust in the organisation.
2.2. Flowchart
See the appendix to this document.
2.3. Reasons for a recall action
A first and most important reason for a recall is to prevent that customers and others experience damages of a product delivered by the certified company through picking up or removing the unsafe product. Therefore the primary goal is the “prevention of damage, accidents or dangerous situations”.
A second reason for a recall action is to satisfy the specific feed safety limits with regard to safety and essential requirements of the GMP+ Feed Certification scheme.
For example:
- the insufficient risk assessment of the product;
- insufficient conditions for the transport of the product;
- the purchasing of raw materials and other ingredients from non-GMP+ (or equivalent) certified companies.
A third reason for a recall action is to protect the image of the product and the company and to prevent sales losses.
2.4. Responsibilities and authorities of the recall coordinator and the recall team
The recall team usually consist of a recall coordinator and staff members. The re-call coordinator is the leader of the recall team and has been appointed. The staff members usually work in the different areas in the company (sections/ departments) such as purchasing, production, quality management, sales, technical service, marketing, finance, administration/customer management, legal services, research and development, and public relations.
The recall coordinator draws up the recall procedure and trains the staff members This person is in charge of a recall action.
The actual decision to proceed with a recall action is made by the -top management Top management carries the final responsibility for the recall action.
The recall coordinator puts together the team and appoints a secretary, who takes the minutes. Besides that, the coordinator can involve external experts in the recall action.
The tasks of the recall team are:
- To determine which products are involved, the quantity of the product, where they are stored, delivered etc. If an adequately functioning tracking & tracing system is present this data will be available very quickly.
- Announcing the recall action (internally and externally including producers, certification bodies, branch organisations, competent authority and so on).
- To set up a procedure for quick and efficient information availability and to direct the recall.
- Drawing up a cost control report
For these tasks administrative employees are added to the team with regard to communication:
- Testing of the quality of the performance of the correcting measures.
- Checking the quantities of the recalled product versus the quantity to be recalled.
- Determining the reimbursement or the replacement product.
- Analysing the reactions of the customers and other persons concerned.
- Analysing the side effects of the recall on the image of the company with regard to customers, parties in the chain, competent authority media, and social organisations.
- Analysing the effects of the recall within the organisation.
- ensuring that the recalled products arrive at their correct destination (return flow, technical destination, destruction, etc.).
2.5. Criteria for starting a recall
Drew up criteria based on the information described in 3.3 and 3.4.
2.6. Planning and establishment of procedures for an effective and fast recall action
A proper traceability system (the tracking & tracing system) is indispensable for performing an effective and fast recall action. See R 1.0 § 8.3 and TS 1.1 § 10 for requirements regarding traceability. For guidelines regarding traceability, see S 9.8 How to develop traceability systems.
2.7. Emergency measures
Write down the possible emergency measures and the information about blocking batches of products, segregation of affected batches, identification of the affected batches.
2.8. Information for employees
It is important that employees are informed about the recall action and what is expected from them.
2.9. External information, customers, parties in the chain, branch organisations, competent authority, media, other persons concerned
Collect all information about the products, external information, information from customers, parties in the chain, branch organisations, competent authority, media, other person concerned.
2.10. Sample texts for press releases, advertisements, warnings, letters
To speed up communication in case of a crisis, sample texts of announcements, press releases, advertisements, warnings and letters can be included in the appendices of the recall procedure. Besides that it contains instructions for telephone operators, advice on how to deal with the media and so on.
2.11. Follow-up lists, lists of contact persons, media lists, lists of external experts
The recall procedure should include an overview of:
- the (deputy) members of the recall team (including the recall coordinator) and their telephone numbers, and e-mail addresses.
- the names and contact details of the external advisors involved in the recall. Examples of external advisors are toxicologists, lawyers, experts in the field of information (public relations) etc.
All components of the recall procedure should be numbered and given to the per-sons concerned and kept up to date.
2.12. Registration of data and experiences
All data and the experiences from the company needs to be registered in order to keep track on all steps.
2.13. Reporting and evaluation
The post recall report should include information about the following items:
- Product: what products were affected by the recall (product description, batch number), distribution list
- Notification: are all customers /public notified, means of communication used, what action was requested from the customers/ public regarding the recalled product. The copies of the notifications should be attached to the report. This also includes press releases and newspaper ads if any.
- Corrective actions: are there corrective actions taken to decrease the chance of the feed safety issue recurring. If yes, what actions have been taken.
- Handling recalled product: what happened with the recalled product. The evidence of the action (e.g. testing, re-processing, relabelling, destruction) should be attached to the report.
- Impact of the recalled product with regard to customers: are there any com-plaints received, animal/ human health issues reported.
- Evaluation of the recall procedure: was it up to date, easy to follow, does anything need to be changed.
After-care
The recall coordinator together with the recall team should ensure that all the data of the recall action is collected, makes up the reports, makes sure that an evaluation takes place and works out the points of improvement. The end result will be pro-cessed in the recall
Appendix Flowchart
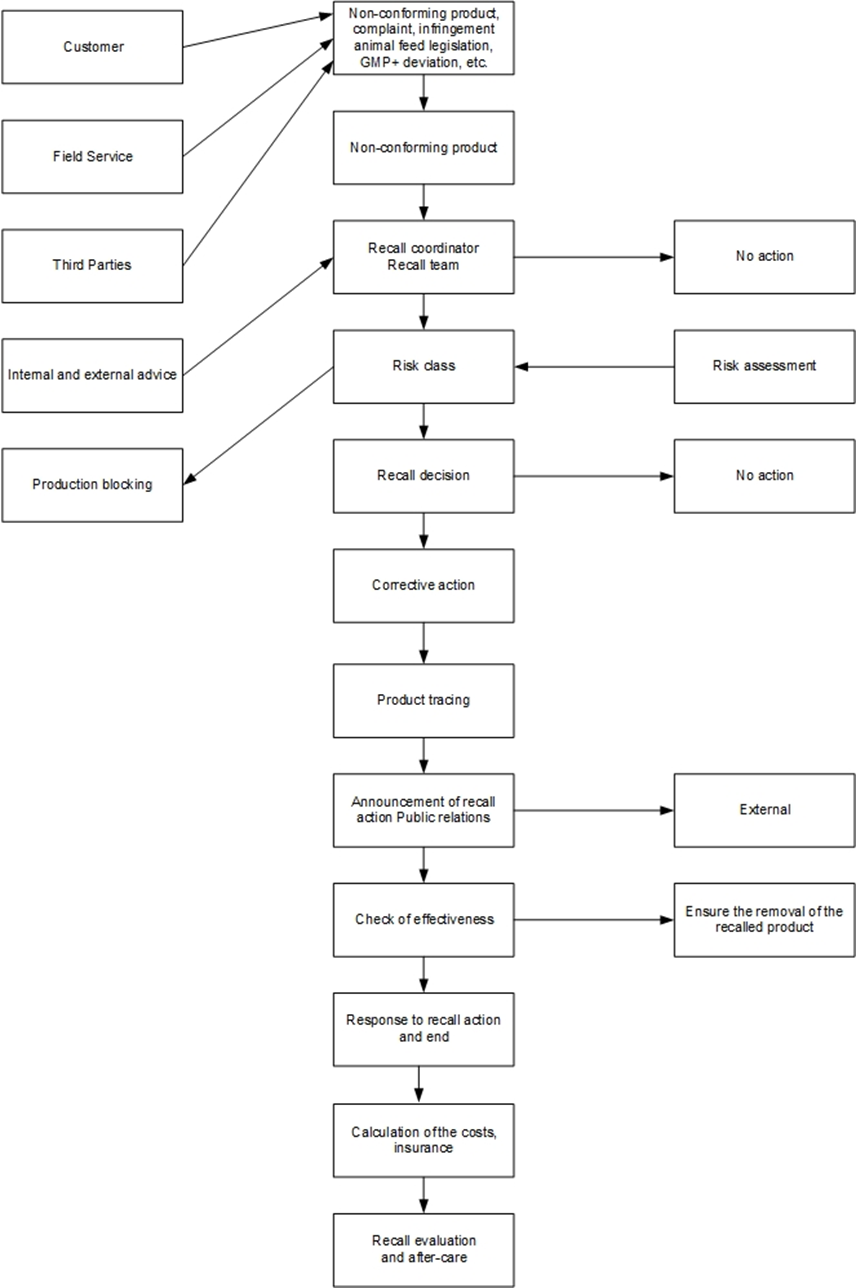