1. Scope of this document
This document enables a company to achieve its feed responsibility objectives. It specifies requirements for a Feed Responsibility Management System (FRMS) which enables a company to provide responsible feed products and feed services.
All requirements in this standard are generic and are intended to be applicable to all companies with activities in the feed chain, regardless of size and complexity. This ranges from companies which produce feed additives, feed materials, premixtures, compound feed or pet food, to companies which are involved in the trade, storage and transshipment and transport by road of these products.
This document allows any company, including smaller businesses, to set up a robust and reliable Feed Responsibility Management System. In addition, internal and/or external resources can be used to meet the requirements of this standard.
If a company demonstrates compliance with the requirements in this standard, a GMP+ FRA certificate can be granted by the certification body.
2. Normative references
The requirements in this document ensure the implementation of a Feed Responsibility Management Systems Requirements (FRMS). The Market Initiative documents contain the responsible feed and feed services requirements set by a particular Market Initiative. The combined use of these documents enables a company to provide responsible feed products and feed services in accordance to the request from the Market Initiative.
This document must always be used in combination with a MI document which holds the requirements set for responsible feed and feed services. The combined use enables a company to provide responsible feed products and feed services in accordance to the request from the Market Initiative.
Both the Feed Responsibility Management Systems Requirements and the Market Initiatives documents must be considered as a normative part of the GMP+ FRA module.
3. Terms and Definitions
See F0.2 Definition list.
4. System requirements
4.1. Feed Responsibility Management System
4.1.1. Compliance with Feed legislation and this Standard
The GMP+ certified company must comply with:
- legislation in the country in which the certified company is located;
- legislation in the country where the feed is marketed.
- the relevant sections of the applied scope(s).
In all of the above cases, the most strict requirement is applicable for GMP+ certified companies.
Helpful tip
Legislation does not have to be only related to feed responsibility legislation. Legislation refers to legal requirements for feed business operators. For example, Reg. (EC) NO. 178/2002 and Reg. (EC) NO. 183/2005. Companies outside the European Union shall comply with the applicable local legislation.
4.1.2. Understanding the Needs and Expectations of interested parties
The certified company must safeguard that the delivered products and services comply with the applicable requirements of the GMP+ FC scheme and the needs from the relevant interested parties.
Helpful tip
There are a wide range of interested parties whose needs you need to think about regarding the GMP+ Feed Responsibility Management System. It can help to list them carefully. These interested parties can range from suppliers, customers, contracted transporters, and providers of services like certification schemes.
4.1.3. Determining the scope of the Feed Responsibility Management System
The certified company must establish, implement, maintain, update and continually improve a Feed Responsibility Management System, in accordance with the requirements of the GMP+ documents. The certified company must comply with the applicable feed legislation and work in accordance with other developments related to their responsibility.
The GMP+ certified company must describe all activities, processes, products or services in the Feed Responsibility Management System (FRMS) for which it is responsible.
The certified company must determine the scope of the FRMS, by specifying:
- all activities, processes, products or services related to responsible feed. These include activities, processes, products and services carried out by/for third parties;
- all locations -- whether these are the property of the company or not -- including relevant administrative locations;
- Which of the activities, processes, products or services related to the production, trade, storage and transport of responsible feed are subject to GMP+ certification;
It is possible to exclude activities, processes, products or services related to the production, trade, storage and transport of responsible feed from the scope of GMP+ certification.
- other (responsible feed and regular feed related) activities, processes, products or services as defined under a) that can have an impact on feed responsibility. The certified company must ensure that these activities, processes, products or services do not have a negative impact on feed responsibility. This must be supported by a risk analysis (§ 4.3).
If a certified company decides to outsource an activity which can have an impact on the production and/or trade of responsible feed, the certified company must ensure that this activity is also carried out in accordance with the requirements of this GMP+ standard.
All activities potentially influencing feed responsibility must be available for auditing. The scope of the FRMS must be documented and updated.
Helpful tip
A great place to start reading about the scope of activities concerning GMP+ certification is the document F0.3 Scopes for certification.
4.1.4. Leadership and Commitment
Top management of a GMP+ certified company must demonstrate leadership and commitment with respect to the Feed Responsibility Management System (FRMS) by:
- ensuring that the feed responsibility policy and the objectives of the FRMS are established;
- ensuring that the resources are made available for compliance with the FRMS;
- communicating the importance of an effective FRMS and by conforming to the FRMS requirements and the mutually agreed customer requirements relating to feed responsibility;
- ensuring that the FRMS is evaluated and maintained to achieve its intended result(s).
4.1.5. Top management’s Responsibilities and Authorities
Top management must ensure that the responsibilities and authorities for relevant roles are assigned, communicated and understood within the organisation.
Top management must assign the responsibilities and authority for:
- ensuring that the FRMS conforms to the requirements as described in this document;
- ensuring that responsible staff are aware of their responsibilities and received appropriate training on methods to comply with the applied scope(s);
- reporting on the performance and any need for improvement of the FRMS to Top management;
-
ensuring that the awareness of the production and/or trade of responsible feed is promoted throughout the whole organisation;
-
in the case of using credits (supply chain models Area Mass Balance and Book & Claim) ensuring that all purchased, redeemed, and sold credits are represented in the material accounting system for the selected reporting period, not limited to the products and/or services linked to the GMP+ FRA activities, but encompassing all credits and claims that can be considered relevant by interested parties.
Top management must declare in writing that they:
- are accountable for the provision of complete, accurate and reliable (sustainability) information;
- will notify GMP+ International and the Certification Body within a timely manner after any sustainability misconduct or fraud (§ 4.8).
4.1.6. Documented information
The certified company’s Feed Responsibility Management System must include:
- documented information required by the GMP+ standard;
- all relevant documented information required by national and international legislation and customers;
- documented information concerning the scope of the FRMS (§ 4.1.3);
- documented information concerning top management’s responsibilities and authorities (§ 4.1.5).
When creating and updating documented information, the certified company must ensure appropriate:
- identification (e.g. a title, date, author, or reference number);
- format (e.g. language, software version, graphics) and media (e.g. paper, electronic);
- review and approval for suitability and adequacy of the information.
Documented information required by the FRMS and by this GMP+ document must be controlled to ensure:
- it is available and suitable for use, where and when it is needed;
- it is adequately protected (e.g. from loss of confidentiality, improper use, or loss of integrity).
For the control of documented information, the certified company must address the following, as applicable:
- distribution, access, retrieval and use;
- storage and preservation, including preservation of legibility;
- control of changes (e.g. version control);
- retention and disposition.
Documented information must be kept at least three years unless a longer storage period is required according to the applicable feed legislation or other regulations.
4.2. Prerequisite programmes (PRPs)
4.2.1. People
The certified company must ensure that the persons who are given the responsibility to operate and maintain an effective FRMS are competent.
The certified company must:
- clearly describe how it organizes its personnel in relation to FRMS;
- determine the necessary competence of persons -- including external providers -- doing work under its control that affects feed responsibility performance and the effectiveness of the FRMS;
- where applicable, take actions to acquire the necessary competence, and evaluate the effectiveness of the actions taken;
- keep appropriate documented information as evidence of competence.
Helpful tip
A competent Feed Responsibility Team has multi-disciplinary knowledge and experience in developing and implementing the FRMS. This includes (but is not limited to) the organization’s products, processes, equipment and feed responsibility hazards within the scope of the FRMS.
The certified company must ensure that all relevant people doing work under the certified company’s control must be aware of:
- the objectives of the FRMS relevant to their task(s);
- their individual contribution to the effectiveness of the FRMS, including the benefits of improved feed responsibility performance;
- the implications of not conforming with the FRMS requirements.
4.2.2. Traceability system
The certified company must have a documented procedure that demonstrates that the certified company is able to ensure the timely withdrawal/recall of products that have been identified as not compliant.
All products that can have an impact on feed responsibility (GMP+ FRA assured or non-GMP+ FRA assured feed) must be traceable in all stages of production, processing and distribution. The traceability system must be able to uniquely identify incoming material from the suppliers and the first stage of the distribution route of the end product.
The required information must be available for GMP+ International and competent authorities within four hours unless the authorities determine a shorter timeframe.
Documented information as evidence of the traceability system must be retained for a defined period, as stated in § 4.1.6. The GMP+ certified company must verify the effectiveness of the traceability system.
Helpful tip
The document Guideline for Traceability Traceability (S9.8 How to develop traceability systems), is very useful and provides more information about how to set up traceability procedure system. Certified companies may use this or a different methodology to set up an internal traceability procedure. The focus of this document is on feed safety, but can be used for feed responsibility as well.
Certified companies must retain the following as documented information for all products and services:
- name and address details of suppliers and customers;
- date of delivery;
- type of product or service;
- product quantity / number of products;
- batch number if applicable. This can also be designated as a producer’s batch number or a reference number;
- transport/ distribution details such as the identification and code of the loading compartments (if the certified company is responsible for transport);
- if applicable: copies of any accompanying documents, warranty statements, certificates etc. in accordance with the arrangements made with the instructing party.
Certified companies must determine whether the documentation of additional details is necessary.
If the certified company is using one of the supply chain models from chapter 5, the records regarding traceability needs to be expanded so it covers all the requirements of the material accounting system (see § 5.1).
4.3. Risk Managment
The certified company must conduct a risk assessment for risks management based on the following principles
- Identification of feed responsibility risk
- establish risks classification (low, medium, high)
- conduct a hazard analysis;
- establish and implement a monitoring system for the identified risks based on the fustified classification;
- define preventive and control measures;
- validate and verify the risk management plan;
- document and register the risk management plan.
In order to apply the principles successfully, the certified company must first comply with a number of requirements including:
- establishing a Feed Responsibility Team;
- specifying products and processes including their use;
- establishing and implementing a prerequisites program (see § 4.2).
Helpful tip
In the case of GMO Controlled and the supply chain model Segregation, the risk of uncontrolled mixing or substitution between responsible feed and regular feed must be identified, classified, monitored, prevented, and controlled. In the case of credit purchase, possible risks must be identified, classified, monitored, prevented, and controlled.
4.4. Purchase
4.4.1. Selection of suppliers
The certified company must ensure that purchased feed and other products and/or services comply with the specified purchasing requirements in the applicable MI document.
The certified company must assess the performance of suppliers at least once a year.
4.4.2. Verification of incoming products and/or services
Certified companies must establish, implement, maintain and update criteria for receiving incoming products and services. The results of entry checks must be retained as documented information.
Each incoming delivery must be verified on the basis of its specifications. The products must comply with the specifications. The relevant supply chain model must be documented.
4.5. Informing the customer
4.5.1. Inform the customer about the status of the feed
The certified company must make the status of the delivered feed or service clear to the customer via a positive declaration. This must be done by using a positive declaration for all feed and services assured under its GMP+ Feed Responsibility Management System. This must include a reference to which of the scopes the feed or service complies with.
The certified company is free to choose how to communicate to the customer about the status of the feed. The positive declaration:
- must be communicated in writing in the official language (or at least one of the official languages) of the country where the feed is marketed or a language understood by the customer;
- must contain wording as described in Appendix 1 or a translation of the English wording;
- be in clear reference to the delivered feed or service;
- is only required if the feed or service is delivered to customers who request feed or service that is compliant with a specific scope
- be unambiguous/clear to ensure a mutual understanding between seller and customer about the status of the feed or service.
Helpful tip
It’s the certified company’s responsibility to make the status of delivered feed or service clear to the customer.
This positive declaration can involve documentation, for example:
- writing down in a contract with the customer which scope the feed complies with;
- confirming the status of the feed on the delivery slip;
- stating that a certain feed recipe complies with the requirements of the specific scope.
4.5.2. Delivery requirements
Certified companies must ensure that for each delivery, the customer that receives feed compliant with the requirements of the applicable scope(s) is informed through a delivery document that must, include the following information:
- name and address details of suppliers and customers;
- date of delivery;
- type of product or service;
- product quantity / number of products;
- the supply chain models (see chapter 5)), and. when two or more batches with different supply chain models are mixed, for each supply chain model. The percentage of responsible feed for the total volume/weight.
Helpful tip
The following feed ingredients are mixed:
- 10% soybean meal with the supply chain model Book & Claim;
- 20% soybean meal with the supply chain model Mass Balance;
- 20% soybean meal with the supply chain model Segregation.
Helpful tip
It’s the responsibility of the certified company to deliver products and inform customers conform their demands. It is the responsibility of the customers to stipulate and inform its supplier on their demands. If the customer demands ‘RTRS B&C soy’, when mutually agreed, the supplier must deliver products conform this demand. In a delivery document, the supplier must make a specification to ‘RTRS B&C soy’.
Certified companies do not have to provide delivery documents with the information described in paragraph 4.5.2.e for feed delivered directly to livestock farmers and/or when compound feed is delivered (Figure 1).
Helpful tip
It’s the certified company’s responsibility to inform the customer. Delivery documentation can include delivery slips, delivery note, Bills of Lading, invoices, shipping documents, and feed accompanying documents.
Figure 1: Required provisioning of the information described in paragraph 4.5.2.e on delivery documentation in different scenarios.
Figure 1 only indicates when certified companies must inform customers on the information described in paragraph 4.5.2.e. All certified companies in the chain must comply with the requirements of the material accounting system in chapter 5.
4.6. Verification
4.6.1. Internal audit
The certified company must conduct internal audits at planned intervals to provide information on whether the FRMS:
- conforms to:
- the certified company’s own requirements for its FRMS;
- the requirements of this GMP+ standard;
- is effectively implemented and maintained.
The certified company must plan, establish, implement and maintain an audit program(s) including a frequency of at least once a year.
The certified company must during the development of the audit program(s) take into consideration:
- the selection of competent auditors who conduct audits which ensure objectivity and the impartiality of the audit process;
- that the results of the audits must be reported to the Feed Responsibility Team and relevant management;
- that documented information is kept as evidence of the implementation of the audit program and the audit results;
- that necessary correction and corrective action must be taken within a determined time frame.
4.6.2. Management review
Top management must review the certified company’s FRMS at planned intervals of at least once a year to ensure its continuing suitability, adequacy and effectiveness.
The management review must include consideration of:
- changes in the organisation relevant to the FRMS;
- information on the performance and the effectiveness of the FRMS, including trends in:
- the compliance with legislation and regulations;
- monitoring and measurement results;
- analysis of the results of verification activities related to PRPs and the hazard control plan;
- audit results (internal and external);
- performance of external suppliers;
- the extent to which objectives of the FRMS have been met;
- the adequacy of resources (e.g. personnel, equipment);
- relevant information obtained through external and internal communication, including requests and complaints related to feed responsibility from interested parties (e.g. customers and suppliers);
- opportunities for continual improvement.
4.7. Communication
4.7.1. General
When determining the internal and external communications relevant to the FRMS, the GMP+ certified company must specify the information to be communicated, the timeframe of communication, the responsible persons, the communication methodology and the target group(s) of the communication.
The GMP+ certified company must ensure that personnel - own and external - related to the FRMS understands the need of effective communication.
4.7.2. External communication
The certified company must establish, implement and maintain effective communications about feed responsibility where relevant as documented with:
- suppliers of products and services and customers about:
- product information to enable the proper handling, storage, distribution and use of the product within the feed chain
- the status of feed and services, and the delivery as described in paragraph 4.5.
- identified sustainability risks as described in paragraph 4.3.
- contractual arrangements, inquiries and orders including their amendments
- feedback -- including complaints
- not meeting requirements or other irregularities / nonconformities (incorrect claims, contamination, commingling, etc.)
- other organizations that are relevant to the FRMS.
4.7.3. Internal communication
The GMP+ certified company must implement an effective communication system to inform on time about feed responsibility issues within the organization, particularly to the Feed Responsibility Team.
The Feed Responsibility Team must include the relevant information when updating the FRMS (§4.1).
Top management must include the relevant information as input to the management review (§ 4.6.2.).
Incident and Crisis Management
Top management must ensure procedures to respond to potential feed responsibility incidents that can have an impact on feed responsibility or to the role of itself in the feed chain.
The GMP+ certified company must keep documented information to manage these incidents.
The GMP+ certified company must:
- respond to incidents/crisis by:
- identifying the applicable legal requirements
- communicating within the company
- communicating to interested parties
- mitigate the consequences of the incident;
- review and, where necessary, update the documented information after the occurrence of any incident.
Examples of incidents related to feed responsibility are double counting, greenwashing, document forgery, incorrect labelling, supply chain fraud, misleading marketing, etc.
Examples of interested parties are described in the Helpful tip of paragraph 4.1.2.
5. Supply chain models
This standard provides various supply chain models. The requirements for application of these supply chain models are explained in this chapter. In the scope of the MI document is laid down which supply chain models can be used.
All supply chain models are documented via the material accounting system. The general requirements regarding the material accounting system can be found in § 5.1. All additional requirements regarding the material account system are described in the paragraph (§) of the applicable supply chain model.
The following supply chain models are stated in these paragraphs (§) :
§ | Supply chain model |
5.2 | Segregation |
5.3 | Mass balance |
5.4 | Area Mass Balance |
5.5 | Book & claim |
Helpful tip
This chapter is a generic chapter used for all FRA scopes (for various types of companies). As a result of this, there can be requirements stated that are not relevant for the certified company applying this standard. In that case these requirements can be skipped. For example there is a reference to conversion factors in the material accounting system. This is only relevant for producers/processers of feed materials.
5.2. Material accounting system
The certified company must set up a material accounting system for recording data related to this standard, including input quantities received and output quantities sold to customers.
The material accounting system must at least include the following information for both input and output:
- product description;
- quantities of certified product (by volume or weight);
- the supply chain model(s) used.
The certified company must draw up once a year volume summaries providing quantities (volume or weight) for each product type and supply chain model. The volume summary for the supply chain models Segregation and Mass Balance must include the following:
- inputs received;
- inputs used for production (only for producers);
- inputs still in stock;
- outputs still in stock;
- outputs supplied.
The volume summary for the supply chain models Area Mass Balance and Book & Claim must include the following:
- credits purchased (to compensate regular feed);
- credits in stock;
- credits redeemed;
- credits sold.
The material accounting system must show which quantities of regular feed were compensated by which credits.
Information in the material accounting system must be transparent and accessible to relevant employees.
Helpful tip
A material accounting system has a clear link with a tracking and tracing system. Certified companies that already use a GMP+ tracking and tracing system (required in the GMP+ FSA module), will find it easy to comply with these requirements.
The certified company must identify all processing steps involving a change of material volume or weight. Changes in quantity of the product resulting from processing must be documented. This must be based either on determining the actual quantity of each subsequent fraction, or on specifying conversion factor(s) for each processing step. Where it’ is not possible to measure each processing step, quantities for the complete process may be used.
If conversion factors are used, the certified company must specify and document the methodology for calculating the conversion factor(s). If the certified company calculates and determines the conversion factor itself, the calculation must be based on the company's available data.
The certified company must ensure that conversion factors are recalculated when there are relevant changes affecting the production process. This must be verified at least once a year.
Toasting, crushing, and drying are examples of processing steps that can involve a change of material volume or weight.
For example, if a certified crusher purchases responsible soy, it will transfer the x amount of soy into a number of fractions (for example soy expeller and soy oil). Within the material accounting system, the certified company can use either actual quantities or conversion factors to transfer responsible input to responsible output.
5.3. Segregation
The certified company must ensure that the responsible feed material supplied to customers has been physically segregated from regular feed material at the physical location. This includes any other stage under the control of the certified company.
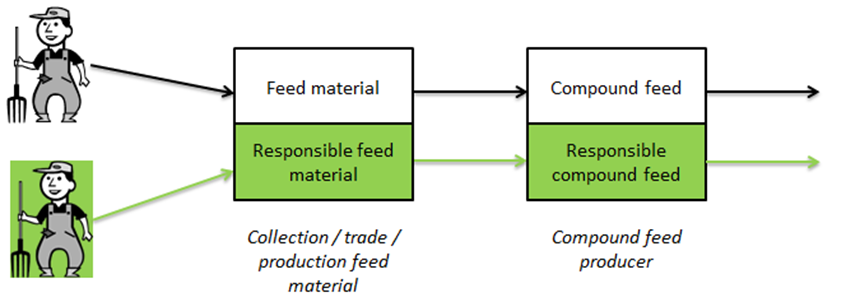
Fig. 2: Schematic overview of Segregation (simplified)
Helpful tip
With the segregated system, the certified company can be certain that the material originates from certified farms. This system is however not an Identity-Preserved (IP) system, so it is not designed to provide traceability back to a specific farm.
5.3.1. Purchasing
Responsible feed material must be sourced directly from certified growers or from suppliers that use the supply chain model identity preserved or segregation.
When the certified company is purchasing feed via multiple supply chain models, the certified company must ensure that inputs to each supply chain model complies with the purchasing requirements in the relevant MI document.
5.3.2. Processing
When identity preserved certified products are mixed with segregated products while abandoning batch traceability, the end product is considered as segregated product.
The certified company must have an effective system in place that is designed to ensure no intermixing between segregated responsible feed material and non-segregated responsible feed material.
Helpful tip
Such a system may include for example allocation adjustments (e.g. that the first flow of product through the system following a change from responsible feed material to regular feed material, can be classified as regular) or other systems. Flushing the processing or storage equipment between flows of responsible feed material and regular feed material can be used as such a system, but physical cleaning is not a requirement for this standard.
5.3.3. Material accounting system
Input
The certified company must record the responsibility data and the quantity (volume or weight) of all responsible segregated input material in the material accounting system, but only after it has gained legal ownership of the input material and has ensured the supporting documentation contains the right information. This data must be recorded as ‘output units’.
Where the processing/production process generates co-products and by-products, the certified company must record the quantity (volume or weight) by using separate categories for these co-products and by-products. In this case conversion factor(s) for the processing unit or actual measured output quantities must be used.
Output
The certified company must deduct the quantity of data supplied to the customers from their material accounting system based on the actual physical material supplied.
Allocation of responsibility data
The certified company must ensure that allocation of data to customers is consistent with the actual physical product delivered.
5.4. Mass balance
The certified company must ensure that the output of responsible feed material supplied to customers does not exceed the input of responsible feed material received at the location, using either a continuous accounting system or a fixed inventory period.
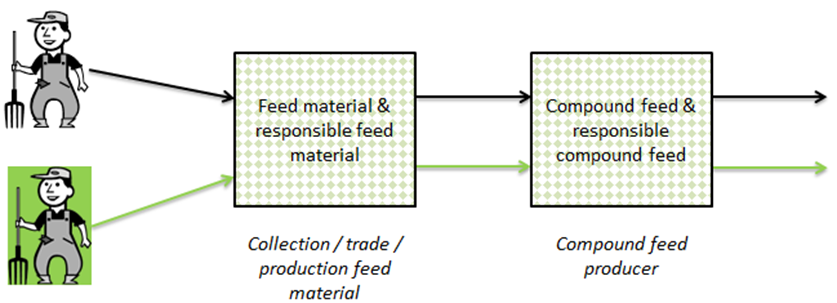
Fig. 3: Schematic overview of Mass balance (simplified)
5.4.1. Purchasing
With mass balance, the certified company is allowed to blend regular feed material with responsible feed material. It is therefore also allowed to purchase regular feed material from suppliers. Responsible feed material must be sourced directly from certified growers or from suppliers that use the supply chain models: identity preserved, segregation or mass balance.
When the certified company is purchasing feed via multiple supply chain models, the certified company must ensure that inputs to each supply chain model complies with the purchasing requirements in the relevant MI document.
5.4.2. Processing
When identity preserved and/or segregated certified products are mixed with mass balanced products while abandoning batch traceability, the end product is considered as mass balanced product. Mass Balanced products cannot be ‘downgraded’ to Area Mass Balanced and Book & Claim products.
5.4.3. Material accounting system
Input
The certified company must record the quantity (volume or weight) of all responsible input material in the material accounting system, but only after it has gained legal ownership of the input material and has ensured the supporting documentation contains the right information. This data must be recorded as ‘output units’.
Where the processing/production process generates co-products and by-products, the certified company must record the quantity (volume or weight) by using separate categories for these co-products and by-products. In this case conversion factor(s) for the processing unit or actual measured output quantities must be used.
Where additional responsibility data is associated with the mass balance inputs received, this data must remain linked, combined and recorded in the material accounting system using separate categories for each identical group of sustainability data.
Output
Where the processing/production process generates co-products and by-products, the certified company must deduct the quantity of data supplied to customers from the respective co-product and by-product categories in the material accounting system. The certified company must not apply data generated from the production of one co-product or by-product to a different co-product and by-product.
Where additional responsibility data is associated with the mass balance inputs received, the certified company must deduct the quantity of data supplied to customers from the relevant category of linked data in the material accounting system.
The certified company must not supply responsibility data to customers for other feed materials. In bulked products, the responsibility data must only be applied to the proportion of the related feed material.
Allocation of sustainability data
The balancing of input and output of responsibility data must be implemented as a part of the material accounting system. Records of responsibility data available for allocation to outputs are clearly visible to relevant personnel and maintained updated at all times.
The certified company must allocate responsibility data to customers using either a continuous balancing system or a fixed inventory period.
Helpful tip
Within the mass balance system it is possible to allocate the sustainability status from one batch to another as long as the certified company doesn’t sell more responsible feed than purchased.
5.4.4. Continuous balancing system
Where a continuous balancing system is in operation, the certified company must ensure that the quantity of physical mass balance material inputs and outputs (in volume or weight) at the physical location are monitored on a real-time basis.
The certified company must ensure that the quantity of material (volume or weight) at the physical location is at least the same as the quantity of responsible feed material (volume or weight) available for allocation to outputs in the material accounting system.
The certified company must ensure that the material accounting system is never overdrawn. Only responsibility data which has been recorded in the material accounting system must be allocated to outputs supplied by the certified company.
Responsibility data is valid for 24 months from the date it was first recorded in the material accounting system. If the certified company does not allocate the available quantity of responsibility data to outputs within 24 months, the data must expire and must be deducted from the material accounting system.
5.4.5. Fixed inventory period
Where a fixed inventory period is in operation, the certified company must ensure that the quantity of mass balance material inputs and outputs (volume or weight) are balanced within a fixed inventory period which does not exceed one year (12 months).
The certified company must overdraw data when there is evidence that purchases are under contract for delivery within the inventory period, to cover the output quantity supplied.
Responsibility data which has not been allocated to output material at the end of the inventory period can be carried over and recorded in the material accounting system for the following inventory period. Carried-over responsibility data is valid for 24 months from the date of the inventory. If the certified company does not allocate the available quantity of responsibility data to outputs within 24 months, the data must expire and must be deducted from the material accounting system.
The certified company must ensure that the material accounting system is not overdrawn at the time of the inventory. Only responsibility data which has been recorded in the material accounting system within the inventory period (including the carried-over from the previous inventory period) must be allocated to outputs supplied within the inventory period.
5.5. Area Mass Balance
The area mass balance model is a combination of Mass Balance (§ 5.3) and Book & Claim (§ 5.5). Collectors/traders that buy feed material on the regular market can purchase ‘responsible feed material production credits’ directly from growers. These credits must however originate from growers that operate in the same area as the feed material is sourced. The certificates from the purchase area are administratively connected to the delivery of feed material from that area via a mass balance model. Therefore, the volume of responsible feed material that is shipped from a specific area can never exceed the volume of credits bought from the growers in that same area.
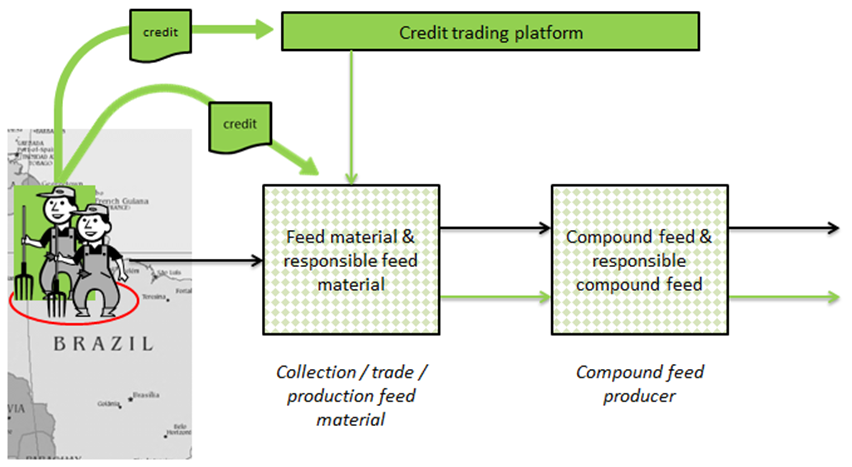
Fig. 4: Schematic overview of Area mass balance (simplified)
Helpful tip
Area is defined as a region / state within a country. In the case of area mass balance, the credits must originate from the same area as the area where the feed material originated from.
5.5.1. Purchasing
With area mass balance, the certified company is allowed to purchase regular feed material from suppliers. Credits must be purchased from a recognized standard as defined in the purchasing requirements of the relevant MI document. These credits must originate from growers that operate in the same area (region) as the feed material is originating from.
When the certified company is purchasing feed via multiple supply chain models, the certified company must ensure that inputs to each supply chain model complies with the purchasing requirements in the relevant MI document.
5.5.2. Processing
When Area Mass Balanced certified products are mixed with Book & Claim products while abandoning the area, the end product is considered as Book & Claim product.
5.5.3. Material accounting system
The area mass balance model has the same requirements for the material accounting system as the mass balance model. The requirements for the material accounting system can therefore be found in § 5.5.2, 5.5.3 and 5.5.4.
Helpful tip
Growers can be granted credits equivalent to the volume of certified production of the raw material. The equivalence of 1 credit is defined by the recognized standard in the relevant MI document. For RTRS, 1 credit is equivalent to 1 ton of RTRS certified soy.
5.6. Book & Claim
The supply chain model book & claim represents the trade of credits through a credit trading platform, where the certificates are separated from the physical flow of feed material. Companies that buy feed material on the regular market can purchase ‘responsible feed material production credits’ directly from growers. These credits equal the responsible production of a certain amount of responsible feed material. After having bought credits, a company can publicly claim to have supported responsible production of equivalent volumes of feed materials.
Via trader:
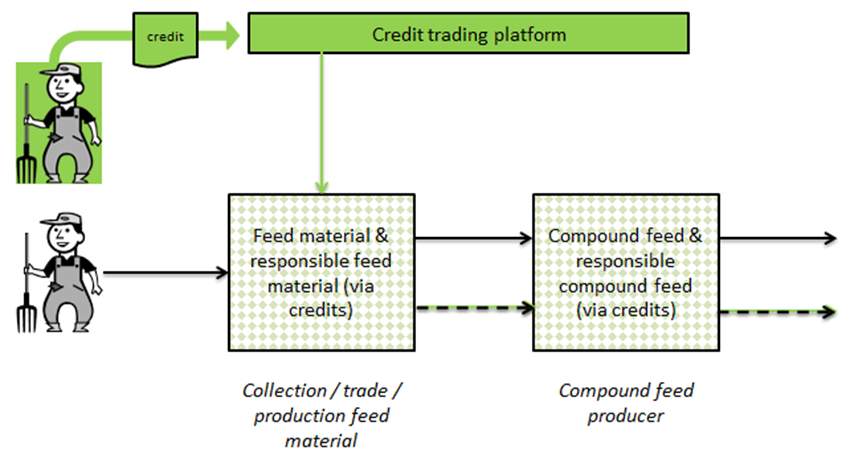
Via compound feed producer:
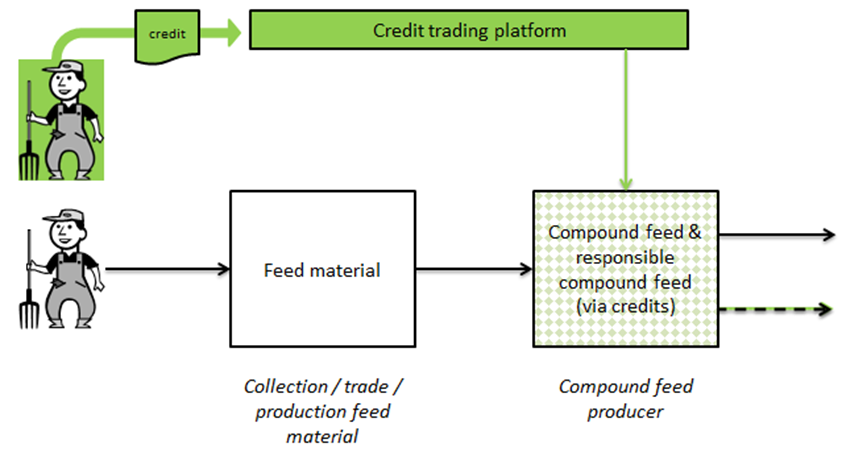
Fig. 5: Schematic overview of Book & claim (simplified)
5.6.1. Purchasing
With book & claim, the certified company is allowed to purchase regular feed material from suppliers. Credits must be purchased via a credit trading platform that complies with the purchasing requirements in the relevant MI documents.
When the certified company is purchasing feed via multiple supply chain models, the certified company must ensure that inputs to each supply chain model complies with the purchasing requirements for that supply chain model.
Helpful tip
In the case that redeeming / claiming of credits is needed to finalize the purchasing process, the requirements regarding purchasing of credits must be read as ‘purchasing including redeeming / claiming’. Otherwise the credits are not considered as purchased and cannot be used in the material accounting system.
5.6.2. Material accounting system
Input
The certified company must record the quantity (volume or weight – as specified on the credit) of all responsible input material in the material accounting system. This data must be recorded as ‘output units’.
Where the production process generates co-products and by-products, the certified company must document the quantity after the production proces by using separate categories for these co-products and by-products. Conversion factor(s) or actual measured output quantities must be used to calculate the quantity after the production process as described in § 5.1.
Output
Where the processing/production process generates co-products and by-products, the certified company must deduct the quantity of data supplied to customers from the respective co-product and by-product categories in the material accounting system. The certified company must not apply data generated from the production of one co-product or by-product to a different co-product and by-product.
The certified company must not supply responsibility data to customers for other feed materials. In bulked products, the responsibility data must only be applied to the proportion of the related feed material.
Allocation of sustainability data
The balancing of input and output of responsibility data must be implemented as a part of the material accounting system. Records of responsibility data available for allocation to outputs are clearly visible to relevant personnel and maintained updated at all times.
The certified company must allocate responsibility data to customers using either a continuous balancing system or a fixed inventory period.
5.6.3. Continuous balancing system
Where a continuous balancing system is in operation, the certified company must ensure that the quantity of credit inputs and outputs (in volume or weight – as specified on the credit) are monitored on a real-time basis.
The certified company must ensure that the material accounting system is never overdrawn. Only responsibility data which has been recorded in the material accounting system must be allocated to outputs supplied by the certified company.
Responsibility data is valid for 24 months from the date it was first recorded in the material accounting system. If the certified company does not allocate the available quantity of responsibility data to outputs within 24 months, the data must expire and must be deducted from the material accounting system.
5.6.4. Fixed inventory period
Where a fixed inventory period is in operation, the certified company must ensure that the quantity of credit inputs and outputs (in volume or weight – as specified on the credit) are balanced within a fixed inventory period which does not exceed one year (12 months).
Responsibility data which has not been allocated to output material at the end of the inventory period can be carried over and recorded in the material accounting system for the following inventory period. Carried-over responsibility data is valid for 24 months from the date of the inventory. If the certified company does not allocate the available quantity of responsibility data to outputs within 24 months, the data must expire and must be deducted from the material accounting system.
The certified company must ensure that the material accounting system is not overdrawn at the time of the inventory. Only responsibility data which has been recorded in the material accounting system within the inventory period (including the carried-over from the previous inventory period) must be allocated to outputs supplied within the inventory period.
Appendix 1: Examples of positive declaration
English
Statements for placing feed on the market | Statements for delivery of service |
The goods delivered are GMP+ FRA assured – Applicable scope name | The service delivered is GMP+ FRA assured – Applicable scope name |
The feed delivered is GMP+ FRA assured – Applicable scope name | The service to be delivered is GMP+ FRA assured – Applicable scope name |
The feed to be delivered is GMP+ FRA assured – Applicable scope name | GMP+ FRA assured – Applicable scope name |
GMP+ FRA assured – Applicable scope name |
|
Risk Management tools
That was a lot of information to digest and one might ask, what is the next step? Luckily we can offer support for the GMP+ Community when doing this. We provide support by means of various tools and guidances but as each company has a shared responsibility to feed safety, and therefor tailor-made solutions cannot be offered. However, we do help by explaining requirements and provide background information about the requirements.
We have developed various supporting materials for the GMP+ Community. These include various tools, ranging from Frequently Asked Questions (FAQ) lists to webinars and events.
Supporting materials related to this document (Guidelines and FAQ’s)
We have made documents available which give guidance to the GMP+ requirements as laid down in the module GMP+ FSA and GMP+ FRA. These documents give examples, answers to frequently asked questions or background information.
Where to find more about the GMP+ International Risk Management tools? Fact sheets More information: GMP+ Platform Product list More information: Product List Risk Assessments More information: GMP+ Platform GMP+ Monitoring database More information: GMP+ Monitoring database Support documents More information: Support documents |