1. Introduction
This document is a stand-alone document which includes a number of best trade practices derived from a HACCP based hazard analysis of the distributive trade sector in compound feed and feed materials.
This standard is based on the former Dutch Guides to good practice as mentioned in the Feed Hygiene Regulation, (Re. EC 183/2005). However, correct application of this standard does not guarantee that the distributive trading company does not have to set up its own HACCP plan. That decision is made by the Competent Authority.
It is a company’s own responsibility to ensure that the processes described in this standard fit in with the companies’ own working methods. If items are not adequately described in this standard, the GMP+ certified distributive trading company (in this document further referred to as certified company) is expected to prepare its own hazard analysis for these items and translate any pursuant action points into control measures for the company.
1.1. Scope and Application of this document
The requirements of this document are applicable to distributive trade companies purchasing feed materials and/or compound feed (in this document further referred to as feed) directly from certified suppliers and selling these directly to livestock farms.
What is in scope?
We clearly discern between distributive trade in packaged feed and bulk feed. A certified company may conduct both forms of distributive trade.
Distributive trade in packaged feed
For packaged feed the following activities are covered by the scope:
- Purchasing from certified suppliers and;
- Transport from producer to storage location and/or sales point of the distributive trading company and;
- Storage at the distributive trading company and;
- Selling (including repackaging) directly to livestock farms and;
- Transport to livestock farms.
Distributive trade in bulk feed
For bulk feed the following activities are covered by the scope:
- Purchasing from certified suppliers and;
- Selling directly to livestock farms.
If a GMP+ certified company carries out activities with feed which are outside the scope of this standard, then it may be necessary to apply another GMP+ FSA standard instead of, or in addition to, this standard. See for exact details F 0.3 Scopes for certification.
Transport and storage can be outsourced to companies with a relevant GMP+ certificate
The certified company may trade in animal feed of non-GMP+ certified suppliers or in non-animal feed (for example veterinary drugs, fertiliser and other items for animals and garden products). The certified company must:
- include this type of trading the Feed Safety Management System;
- keep (feed and non-feed related) activities, processes, products or services which are not covered under the scope of GMP+ certification totally separate, both in physical and administrative terms, from trading in GMP+ assured feed;
- where necessary, implement and monitor other control measures, based on a HACCP analyses, to ensure that GMP+ assured feed is not negatively affected by above-mentioned activities, processes, products or services.
All activities potentially influencing feed safety must be available for auditing.
1.2. The structure of this document
This standard is structured in a specific way. It consists of two more general chapters followed by Chapter 3, Chapter 4 and Chapter 5 containing detailed requirements for the certified company. Chapter 6 contains registration forms that certified companies may use in their daily business in applying the requirements included in the Chapters 3, 4 and 5 of this document.
GMP+ Technical Specifications to which there are also references, are separate GMP+ documents.
When this standard makes a reference to such a GMP+ document, the GMP+ certified company must ensure that the requirements from that document are met. These documents can be found on the GMP+ International website (www.gmpplus.org).
For the explanatory list of relevant terms and definitions see F 0.2 Definition list.
1.3. Exclusion of requirements
It is possible that certain requirements do not apply to a certified company. In that case, a certified company may exclude those specific requirements. Exclusions must, however, be justified and recorded. The exclusions may not, in any event, lead to the participant supplying feed which does not comply with feed safety as defined in the GMP+ FSA module.
Requirements may not be excluded because the certified company does not consider them to be relevant. For example, because customers do not ask for them, or because compliance with these requirements is not a legal obligation; or because the certified company considers itself too small.
2. Normative references
The certified company must comply with the limits and requirements as recorded in the feed legislation and regulations. The limits are listed in a GMP+ document with the title TS1.5 Specific feed safety limits. The overview below includes the most applicable feed regulations.
Number | Referring to: | Official title |
- | Regeling diervoeders | |
178/2002 | (General Foodstuffs Regulation) | Regulation (EC) Nr. 178/2002 of the European Parliament and the Commission of 28 January 2002 to determine the general principles and requirements of the foodstuffs regulations, to form a European Authority for Food Safety and to determine procedures for food safety issues. |
183/2005 | Animal Feed Hygiene Regulation | Regulation (EC) Nr. 183/2005 of the European Parliament and the Commission of 12 January 2005 to determine the requirements for animal feed hygiene. |
2002/32/EC | Undesirable substances | Directive 2002/32/EC of the European Parliament and of the Council of 7 May 2002 on undesirable substances in animal feed. |
999/2001 | Animal proteins | Regulation (EC) No 999/2001 of the European Parliament and of the Council of 22 May 2001 laying down rules for the prevention, control and eradication of certain transmissible spongiform encephalopathies |
- | Besluit Diergeneesmiddelen | Government decree of November 2nd 2012 regarding additional rules for veterinary medicine |
Keep in mind that existing legislation often changes. All later relevant changes to the original legislation can be found in so-called "consolidated law" texts. However, these consolidated versions do not have an official status. They are also generally not updated to include the most recent changes in legislation. The introductory section to the consolidated law texts lists the most recent changes it includes. To enhance transparency, this document exclusively mentions the original legislation, rather than the changed legislation.
Please note: current feed legislation can be consulted via the following link
3. HACCP system requirements
3.1. Responsibility of the management
3.1.1. General
The certified company must always be aware of its responsibility for feed safety during the period in which the feed is traded and when the certified company collects, stores, keeps, repackages and delivers packaged feed.
The certified company must ensure that these activities are controlled and carried out in such a manner that any hazards that may affect feed safety will be prevented, eliminated or reduced to a minimum.
- The certified company must describe its activities (see Chapter 5, process control overview);
- Activities that are not in scope of this document (including storage of fertiliser and pet food) must not have a negative impact on feed products.
For a description of activities, the certified company may use registration form 1 (Chapter 6).
3.2. Quality manual
In order to be able to guarantee feed safety, the certified company must have minimum procedures in place with respect to documentation, registration, identification, traceability, complaints registration and product recalls.
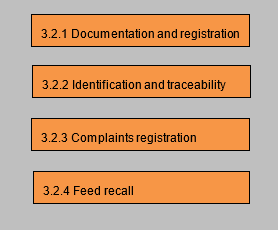
3.2.1. Documentation and Registration
The certified company must have a documentation system in place in order to determine and control critical points in distributive trade.
The company must maintain a register with required documentation, the required registrations and inspections. Registrations must be determined and updated in order to provide proof of compliance with requirements in this document in order to guarantee feed safety.
The certified company must prepare and update a manual. This manual must contain or refer to at least the following documentation where applicable:
- A description of all activities of the certified company as required under § 3.1.1;
- Documented procedures as in § 3.2 and;
- Any other documents that the certified company should require for realizing an effective planning, execution and control of the distributive trade;
- Registrations required by this document;
- Registrations of inspections and analysis results;
- All relevant legally required permissions, registrations and certifications pursuant to the feed legislation and regulations.
- Registration of inspection reports and certificates in the context of the GMP+ Feed Certification Scheme
A documented procedure must be set up for control, identification, storage, protection, finding, duration of storage and destruction of registrations. The following minimum requirements apply:
- Registrations must be legible, easily identifiable and easy to find;
- The retention period for registrations is at least three years, unless a longer retention period is required by law or other regulations;
The above documents and registrations must be easily accessible and shall be made available to the competent authorities at their request.
3.2.2. Identification and Traceability
Feed must be traceable from the moment of purchase, up to sale and including transport. The certified company must at least include the following details in its records:
Purchasing:
- Name, address and telephone number of suppliers of compound feed and feed materials;
- Date of delivery;
- Type of feed and composition (the certified company may use the information from product specifications received from its suppliers);
- The quantity of each feed delivered;
- Charge number if applicable. This is also referred to as the reference number, batch number or lot number.
Most of this information will be available on the purchase orders, which must be retained
Repackaging:
- Date of breaching sack;
- Type of feed;
- Charge number if applicable. This is also referred to as the reference number, batch number or lot number.
Sale:
In order to limit damage as much as possible in the event of calamities, the certified company shall make a reasonable effort to register the following details of its livestock farm customers:
- Name, address, telephone number and official identification number of customers;
- Date of delivery;
- Type of feed;
- The quantity of each feed delivered;
- Charge number if applicable. This is also referred to as the reference number, batch number or lot number.
- Carriers (if applicable).
Professional livestock farms have a official identification number. All other customers are regarded as hobby livestock farms.
3.2.3. Complaints and Incidents registration
The certified company must set up a system for the registration and processing of complaints or incidents. It is possible that a complaint or incident is such that it results in a feed safety hazard. In some cases, the applicable standards are not complied with. Other cases may concern complaints or deviations, such as non-conforming packaging, incorrect delivery, exceeding the feed guarantee date, deviations in transport, detected pests etc. The certified company must then implement control measures in order to prevent or control the detected hazard.
They way complaints or incidents with respect to feed are interpreted or processed depends on the complaint. There may be a shared responsibility between the certified company and its supplier. Consultation with the supplier may be necessary. In all cases, the certified company must:
- Register the complaint / incident;
- For registration and processing of complaints, the company may use registration form 2.
- Contact the feed supplier;
- In consultation with the supplier, derive the root cause and take corrective measures;
- Register the corrective measures taken;
This can also be reported by the supplier. The certified company must in that event retain a copy of the supplier’s report in its records. - Receive feedback in writing from the supplier with respect to the final process/resolution and completion of the report.
Early Warning System (EWS)
- In the event of a potential hazard that cannot be controlled by either the certified company and/or the supplier, and that may also cause damage to other parties, the complaint must be reported to GMP+ International (in the context of the Early Warning System). Consultation with GMP+ International is necessary to check if this has consequences for the relevant feed.
- Registration form 3 must be used in all cases if a complaint / incident is reported to GMP+ International.
3.2.4. Feed recall
The certified company must have a fast recall procedure and implement this in the event where an feed is discovered that is unsafe for either humans and/or animals. This may occur after a complaint or an incident (see § 3.2.3) or at the request of the feed supplier. Recalling feed, depending on the complaint, is a shared responsibility. The supplier needs the certified company’s information and vice versa. Consultation with the supplier may be necessary.
Before any recalled (returned) feed is put back onto the market, the certified company must reassess these using a quality control procedure (see § 5.2.1).
The certified company should take the following measures in consultation with the supplier:
- Immediately, possibly after receiving a request to that effect from the supplier, supply information regarding one or more shipments delivered. This concerns the information stated in § 3.2.2: Name, address, telephone number and if applicable official identification number of customers, delivery date and quantity;
- Immediately inform the private persons/customers/ general public regarding unsafe feed
- Immediately block the feed or have it blocked;
- Recall the feed and return these to the supplier. Appendix 1 includes guidelines for a recall plan.
If consumption of a feed may lead to adverse effects for human or animal health and the customers of this feed cannot all be contacted directly, the company must warn feed customers via the media. Depending on the spread area of the product, regional or national newspapers may be used, always in combination with a press release. See Appendix 1 for an example of such an advertisement.
3.3. Verification (internal audit)
In order to check compliance with the requirements in this document the certified company must verify the system by means of analysis and/or assessment via an internal audit. The certified company may use registration form 4 for conducting such an internal audit.
The verification (internal audit) must be conducted at least once in 12 months. If the answer to any of the questions is “no”, the company must take corrective measures and check their effectiveness within one month of their implementation. This working method is to be repeated until full compliance with requirements is achieved.
4. Prerequisites
The prerequisite programme for distributive trade in feed consists of 5 components as indicated in the diagram below.
4.1. Personnel
The certified company and its personnel carrying out activities that may influence feed safety must be sufficiently knowledgeable, skilled and competent. Additionally, the certified company and its personnel must be aware of the importance of their activities relating to feed safety.
- This may be based on a certificate or equivalent experience in the field of feed safety.
- Updating knowledge by means of literature and courses in this field is desirable. This also applies to temporary staff;
- The certified company must record the responsibilities and authorisation levels of each employee in a registration form, as well as their training and professional experience levels.
- Where relevant, quality control must be assigned to a person with the required qualifications.
- All personnel must be informed in writing of their tasks, responsibilities and authorisation level with respect to feed safety.
Registration form 5 specifies the above-mentioned items.
4.2. Company premises
The company premises must be laid out and maintained in such a way that:
- The risk of mistakes is minimised and contamination, cross-contamination and general deterioration of the feed safety and quality are prevented as much as possible;
- Any ambiguity between different products is prevented, the products are easy to identify and cross-contamination and deterioration are avoided.
General:
- Feed must be stored in clean and dry spaces;
- The storage space must be in excellent state of maintenance;
- The storage space must be lit by sufficient daylight and/or artificial light in order to ensure work can be carried out in good order.
- Where necessary, the temperature must be kept as low as possible in order to prevent condense and decomposing;
- The storage spaces must be accessible exclusively to persons with the company’s permission.
Windows, doors and other openings:
- Windows and other openings must be constructed to bar any hazardous organisms. Doors must close properly and, when closed, must be impenetrable to hazardous/harmful organisms and pests. All openings must be closed as much as possible as activities allow. Windows must, if necessary, be equipped with insect screens;
- Where closing is not an option, or not always possible (for example in the case of fans, doors etc.), measures must be implemented (for instance in the form of plastic flaps or screen doors) in order to limit access opportunities to pests.
Ceilings:
- Where necessary, ceilings and ceiling elements must be designed, constructed and finished to prevent dirt from accumulating and to limit condensation, undesired fungal growth and loose particles, which may affect the safety and quality of the feed.
4.3. Pest control
The certified company must prevent any animals, pests or excrement from coming into contact with the (stored) feed. The certified company must prepare a pest control plan:
The pest control plan must at least include the following elements:
- The types of pests that are controlled by the plan;
- The tools and substances used to prevent and counter the presence of pests; only permissible agents are used for pest control and extermination.
- Where (and with which frequency) the measures must be carried out.
For registration of data, the company may use registration form 6.
If a professional pest control and extermination company is used, retaining the registration sources issued by the pest control company will suffice.
Pest control must be carried out by either an official pest control company or sufficiently qualified and certified personnel.
Consult the latest update of permissible pest control and extermination agents in the database of College voor de toelating van gewasbeschermingsmiddelen en biociden (the Dutch Board for the Authorisation of Plant Protection Products and Biocides, Ctgb) on the internet: https://english.ctgb.nl/
4.4. Cleaning and Disinfection
Deterioration and dust must be prevented and controlled in order to prevent hazardous organisms from entering the feed.
Cleaning programmes must be implemented in respect of the feed storage spaces (intermediate storage and point of sale), as well as the spaces where waste is stored (see § 4.5). Where applicable, traces of cleaning and disinfection agents must be minimised.
The cleaning programme must at least include the following elements:
- The responsibilities with respect to cleaning;
- Description of the relevant spaces;
- The frequency of cleaning;
- Application of various cleaning and disinfection regimes depending on the feed products;
- Cleaning and disinfection agents. These must be suitable for the purpose of actual use. Additionally, these must not form a risk to feed safety.
For registration of data, the company may use registration form 7.
4.5. Waste and Toxic material
Waste and toxic material (including crop protections agents, cleaning agents, pest
control agents, fertilisers and manure) must be:
- visually marked as such and
- shielded in order to eliminate the risk of accidents or unintended use.
In addition, waste must be:
- collected or stored in separate containers. The containers must be easy to identify and must be covered if the waste could attract pests and insects;
- stored separately from animal feed;
The GMP+ certified distributive trading company must make clear how waste and waste removal are controlled. The certified company must be able to demonstrate that waste has not entered and cannot enter the animal feed chain. Customer receipt slips must always be retained.
5. Process control
The critical points in the process have been determined on the basis of a generic specification of HACCP steps for distributive trade in the feed sector and general control measures have been set out - see the summary.
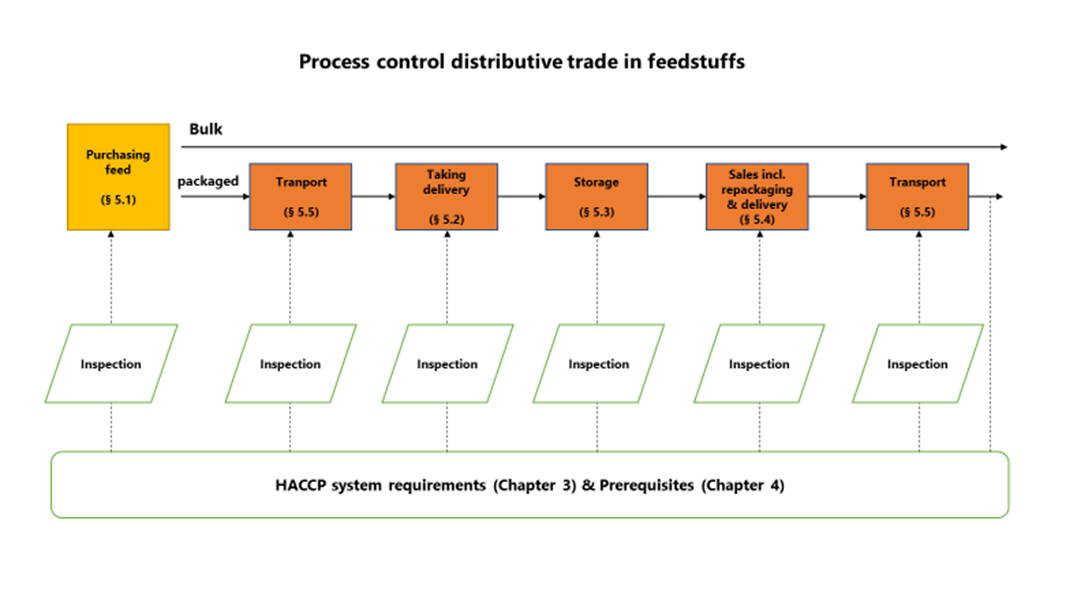
Summary of hazards, control measures, monitoring and corrective measures | |||||||||
PROCESS STEP | DESCRIPTION OF HAZARD | RISK ASSESSMENT | TYPE OF CONTROL MEASURES | MONITORING | FREQUENCY | CORRECTIONS/ CORRECTIVE ACTIONS | REGISTRATION | ||
| | LIKELYHOOD / OCCURANCE | SEVERITY | RISK CAT | | | | | |
Purchasing (par 5.1) | Feed does not comply with legal and GMP+ requirements | small | high | 3 | Exclusively purchasing compound feed and feed from companies certified or registered under FH Exclusively purchasing compound feed and feed from GMP+ certified suppliers | Does supplier have valid registration or certification Does producer have GMP+ or equivalent certificate | At least once in 12 months | No purchasing | Register deviations on registration form 8 |
Transport Supply (par 5.5) | (cross) contamination product | medium | medium | 3 | Inbound and outbound transport of packaged feed in own management -load space must be clean and dry -load space must be completely empty and free of load residue and smell of previous loads -when combining loads, keep feed separate | Visual inspection of load space | For each loading of load space | No loading. Clean load space before loading. | Register deviations on registration form 8 |
| | small | medium | 2 | Delivery of bulk and packaged feed by third parties - exclusively by registered or certified carriers working in accordance with the Road Transport guide. - Bulk: Exclusively GMP+ certified carrier | Does carrier have valid registration or certification? Check if the company fulfils the agreement | At least once in 12 months | Do not use again. | Register deviations on registration form 8 |
Taking delivery (par 5.2); | Loss of quality | small | medium | 2 | -Packaging clean and intact -Not past guarantee date | Visual inspection | All deliveries | Remove as waste or; Return to supplier | Register deviations on registration form 8 |
Cross-contamination / contamination | small | medium | 2 | - return of feed that was in contact with animals cannot be accepted | Assess if return is possible | All returns | Remove as waste or return to supplier | Register deviations on registration form 8 | |
Storage (par 5.3); | Loss of quality and Cross-contamination | small medium | medium medium | 2 3 | Storage of packaged feed in own company premises -repair/remove broken packaging -do not place packaging on the ground -labels legible -do not exceed guarantee date, supply based on FIFO -separate storage for feed and non- feed | Visual inspection of packaging | Frequently, at least once in 12 months | Remove as waste or; Return to supplier Separate and check if products are not contaminated. If contaminated, remove as waste | Register deviations on registration form 8 |
| small | medium | 2 | Storage of bulk and packaged products by third parties - exclusively by registered or certified storage companies working in accordance with FH. - Packaged: Exclusively for companies complying with requirements 5.3.1 which have a contract. - Bulk: Exclusively GMP+ certified storage companies | Does storage company have valid registration or certification? Check if the company fulfils the agreement Does storage company have GMP+ or equivalent certificate? | Frequently, at least once in 12 months | | Register deviations on registration form 8 | |
Sales (incl repackaging and delivery) (§5.4) | feed not suitable for animal species | small | high | 3 | -sell feed intended for animal species as stated on packaging and/or product specification sheet | Checking information on label / product specification sheet | All sales | Accept return and/or contact supplier to determine corrective measure | Register deviations on registration form 8 |
Transport outbound | See transport inbound | medium | medium | 3 | See transport inbound | See transport inbound | See transport inbound | See transport inbound | See transport inbound |
5.1. Purchasing
The certified company exclusively purchases compound feed and/or feed materials from suppliers that are certified with a GMP+ certificate (scope: Production and /or trade in feed), or with an equivalent certificate:
- Keep a copy of the certificate in the records. This is not necessary if the producer is included in the GMP+ International database, see www.gmpplus.org.
- Frequently check if the supplier still complies with the applicable requirements, for example once in 12 months.
- Any irregularities regarding purchasing must be registered on registration form 8.
5.2. Taking delivery of packaged products at own company premises
The certified company may exclusively take delivery of (packaged) feed if these comply with the applicable requirements in order to prevent loss of quality, cross-contamination and/or (hazardous) contamination in subsequent stages of the process.
- The packaging material of feed must be clean and intact on delivery. Check the packaging of each delivery;
- Check if the feed has a label. If not, contact the supplier;
- The feed must not be past their guarantee date. Check the guarantee date of feed of each delivery.
- If a feed or the packaging does not comply with requirements, it must be removed or returned to the supplier (depending on the agreements with the producer);
- Any irregularities regarding taking delivery must be registered on registration form 8.
5.2.1. Returns
In the event of a possible return (e.g. due to errors in the order procedure), the certified company must assess which actions must be taken.
- The certified company must assess if returns are possible due to errors in the order procedure (feed must have the original, clean and unopened packaging with the original label; feed has not been in the stables and was not in contact with animals, etc.);
- In order to prevent germs and diseases spreading, packaged feed that has been in contact with animals will not be accepted as a return. This feed must be easy to identify and must be considered as waste;
- Returns must be registered. Registration form 8 may be used to describe this registration (including the cause).
5.3. Storage
5.3.1. Storage of packaged feed at own company premises
The (packaged) feed purchased by the certified company must be stored in such a manner that loss of quality, cross-contamination and/or (hazardous) contamination are prevented.
- The feed must be stored and delivered in accordance with the FIFO principle as much possible. Ensure that the date of entry or a lot code is stated on the package if the supplier has not already done this;
- Place the animal feed not directly on the ground. Use pallets or racks, for example;
- In order to prevent cross-contamination, animal feed must not be in contact with non-animal feed products, including crop protection agents, cleaning agents, pest control agents, fertiliser, manure etc.
- GMP+ assured feed must not be come into contact with non-GMP+ assured feed.
Inspection of feed:
- Frequently check the packaging and the label. The packaging must be clean and intact. Repair broken packaging or remove broken bags (see § 4.5);
- Labels must be clearly legible;
- Frequently check if the feed is not past its guarantee date;
- Any irregularities regarding storage and delivery must be registered on registration form 8.
5.3.2. Storage of Bulk and Packaged feed products by third parties
If the certified company outsources storage to an external (storage) company, then:
Packaged:
- The (storage) company does not need to be GMP+ certified, but must comply with the requirements applicable to storage at own premises, see § 5.3.1.
- The distributive trading company must make agreements to this effect with the (storage) company. These agreements must be recorded in a contract. An example of such a contract is included in Appendix 2.
Bulk:
- The (storage) company must be GMP+ certified for scope Storage, or;
- Must be certified with an equivalent certificate;
- A copy of the certificate must be present in the company’s records. This is not necessary if the (storage) company is included in the GMP+ International’s company database, see www.gmpplus.org.
- The certified company must frequently check if the (storage) company still complies with applicable requirements, for example once in 12 months.
- Any irregularities regarding external storage must be registered on registration form 8.
5.4. Sales (including repackaging and delivery)
The certified company exclusively sells feed to livestock farms. The feed must be suitable for the intended species.
- In the event that products are repackaged, the label data of the relevant feed must be available for inspection at the point of sale. This means that above each shelf, or at the cash register, a sign must state that the label data of the relevant feed can be viewed at request and are available in a folder. Alternatively, these may be available in digital form and can be printed on request;
- Feed that has almost past its guarantee date may be delivered only if the feed is certain to be fed to the animals before the guarantee date.
- See TS 1.8 Labelling for additional requirements regarding trading GMP+ assured feed and additional labelling requirements.
- Any irregularities regarding sales must be registered on registration form 8.
5.5. Transport
5.5.1. Inbound and Outbound transport of packaged products in own management
If the certified company transports the packaged feed to the own company and/or to the customer, the loading compartment and technical tools of the transport vehicle(s) used must be clean.
- The load space must be clean and dry;
- The load space must be completely empty and free of load residue and smell of previous loads;
- If the load space does not comply with the requirements under a) and b), cleaning is required. The load space must at least be swept out;
- In the event of combined loads of feed and other products/materials, cross-contamination must be prevented;
- Any irregularities regarding transport must be registered on registration form 8.
5.5.2. Delivery of Bulk and Packaged products by third parties
If the certified company outsources transport to an external (transport) company, then:
Packaged:
- The (transport) company must be certified for scope Road Transport –or;
- The transport) company is not GMP+ certified, but must comply with the requirements applicable to transport under own management, see § 5.5.1.
- The certified company must make agreements to this effect with the (transport) company. These agreements must be recorded in a contract. An example of such an agreement is included in Appendix 3.
Bulk:
- The (transport) company must have a scope Road Transport – or an equivalent certificate;
- A copy of the certificate must be present in the certified company’s records. This is not necessary if the carrier is included in the GMP+ International’s company database, see www.gmpplus.org.
- The certified company must frequently check if the (transport) company still complies with applicable requirements, for example once in 12 months.
- Any irregularities regarding external transport must be registered on registration form 8.
6. Registration forms for the distributive trade standard
These registration forms are an important part of process control. These serve to demonstrate that the procedures described were carried out. The registration forms are provided as examples only. If a company has its own forms that provide the same or more extensive information, the use of such in-company forms is permitted.
Please note: Make copies of the forms.
The following registration forms are available:
Registration form 1 - activities distributive trading company
Registration form 2 - complaints registration form
Registration form 3 - EWS Notification form
Registration form 4 - questionnaire internal audit and verification
Registration form 5 - overview of employees
Registration form 6 - pest control
Registration form 7 - cleaning
Registration form 8 - deviation situations
REGISTRATION FORM 1: ACTIVITIES DISTRIBUTIVE TRADING COMPANY
Address details | ||
Name of company / organisation Street + Nr. :……………………… Postcode Town: Telephone number(s) If applicable: (Intermediate) storage location Street + Nr. :……………………… Postcode Town:………………………… Telephone number(s) :……………………… Location point of sale Street + Nr. :……………………… Postcode Town:………………………… Telephone number(s) :……………………… □ Tick for multiple points of sale Add a separate address list as an Annex | ||
Feed | ||
| Activities | Products |
Bulk | □ Purchasing - selling □Transport (outsourced) □ Storage (outsourced) | □ Feed * □ Compound feed * |
Packaged feed | □ Purchasing - selling □ (Intermediate) storage (own management) □ Storage point of sale □ Storage (outsourced) □ Repackaging □ Transport (own management) □ Transport (outsourced) | □ Feed * □ Compound feed * |
□ Tick if non-GMP+ assured feed is traded here as well. Add a separate list of activities and product types as an Annex. | ||
Other products Please note: These products must not have a negative effect on feed | ||
| Activities | Products |
| □ Purchasing - selling □ (Intermediate) storage (own management) □ Storage point of sale □ Transport (own management) | □ Fertiliser □ Veterinary drugs □ ……………………… □ ……………………… |
*: The specifications of this feed is described on the packaging or on attached documents (for bulk products).
Date:…………………………….. Signature :…………………………….
REGISTRATION FORM 2: COMPLAINTS REGISTRATION FORM
Number : …………..
Sender : ………………………………………………….. Date: …………………..…….......
________________________________________________________________________
Customer – supplier name:…..…..…………..…....................................................................
Contact person:…………..….................................................................................................
Position: ……… ………………….. Tel: …………………........................................
_______________________________________________________________________
DESCRIPTION OF COMPLAINT Internal / External
……………………………………………………………………………………………..……………
……………………………………………………………………………………………..……………
……………………………………………………………………………………………..……………
……………………………………………………………………………………………..…………..
Relates to department........…………………………………………………………………………
Dossier number:………………………………………………………..........................................
Date registered in complaints register:......………………..……..…........................................
Initials for receipt of complaints registration form:...………………..……..…..........................
Action to be taken by:.........................…………………..…………..........................................
Department:...........………………….........…………..……..……………………………………..
_______________________________________________________________________
DESCRIPTION OF ACTION TAKEN
……………………………………………………………………………………………..……………
……………………………………………………………………………………………..……………
……………………………………………………………………………………………..…………....
Date action completed:....................……………………………………..…………………………
Date action reported to customer..........……………………………………………………………
Initials:...............……….....................……………………………………....................................
_________________________________________________________________________
Complaints register filing date:……….....................…………...................................................
Initials for receipt:…………..........…………..……..…...............................................................
REGISTRATION FORM 3: EWS NOTIFICATION FORM
You must fill out the form digitally via this LINK
The timely and complete notification of exceedance of the maximum permitted level(s) of undesirable substances in feed is of great importance. In practice, it may sometimes be difficult to fill out the EWS Notification Form completely at the first notification because not all necessary details are available. The first notification must in that case contain at least the details that are indispensable for a proper first assessment of the incident. Subsequently, the participant must supplement and submit the missing details as soon as possible.
REGISTRATION FORM 4: QUESTIONNAIRE INTERNAL AUDIT AND VERIFICATION
This form must be completed once every 12 months.
If the answer to one or more questions is “No”, you are required to complete another questionnaire after one month.
Date:
Question | Requirements described in: | Yes / No / N/a | Measure to be taken after deviation |
HACCP SYSTEM REQUIREMENTS | | | |
1. Were the activities described, see registration form 1? | | | |
2. Is a manual available with the following procedures: Documentation and registration □ Identification and registration □ Complaints registration □ Early Warning System □ Feed recall □ Verification | | | |
3. Were all documents and registrations updated and retained for at least 3 years? □ inspections □ Analyses and certificates □ Permits, registrations and certifications | | | |
4. Were the details of all suppliers and feed entered in the records? □ Name and address details □ Date of delivery □ Type of feed, composition □ quantity □ Applicable transport □ Charge number if applicable (reference number, batch number, lot number) | | |
Question | Requirements described in: | Yes / No / N/a | Measure to be taken after deviation |
5. Were all the details of the feed entered in the records if concerning repackaging? □ Date of breaching sack □ Type of feed □ Charge number if applicable (reference number, batch number, lot number) | | | |
6. Were adequate efforts made in order to register the details of professional livestock farms? □ Name and address details, telephone number and official identification number □ Date of delivery □ Type of feed □ quantity □ Charge number if applicable (reference number, batch number, lot number) □ Carriers | | | |
7. Was a system set up for registration and processing of complaints or calamities? □ Registration of complaints and actions taken (registration form 2) □ Consultation with the supplier (including feedback regarding completion of the Notification) □ If necessary, notification to competent authority | | | |
8. Was a recall plan in writing available and does it contain the minimum required elements? □ Supply information regarding customers (including official identification numbers) □ Inform the customer immediately □ See Appendix 1 for further interpretation and details. | | | |
9. Verification (see bottom of this questionnaire Record conclusion). □ Is this questionnaire be completed at least once in 12 months? | | | |
GENERAL REQUIREMENTS | | | |
Personnel 10. Are the certified company and its employees carrying out activities that may influence feed safety sufficiently knowledgeable, skilled and competent? See registration form 5 | | | |
11. Was each employee instructed in writing regarding his/her tasks, responsibilities and authorisation level regarding feed safety? See registration form 5. | | | |
Company premises (only for storage under own management) 12. Is the risk of mistakes (confusion between products) minimised and are contamination, cross-contamination and general deterioration of the feed safety and quality prevented as much as possible?
| | | |
Question | Requirements described in: | Yes / No / N/a | Measure to be taken after deviation |
Birds, pets and pests (only for storage under own management) 13. Does the company prevent any pets, birds, pests, insects or any excrement from coming in contact with the (stored) product. 14. Was a pest control plan prepared? See registration form 6. | § 4.3 | | |
Cleaning and disinfection (only for storage under own management) 15. Is a cleaning programme implemented for the feed storage spaces and the waste storage space? See registration form 7. 16. Are traces of cleaning and disinfection agents reduced to a minimum? | | | |
Waste and toxic material (only for storage under own management) 17. Are waste and materials that are not suitable as feed kept separate and are these identified as such? | | | |
PROCESS CONTROL | | | |
18. Is a hazard and risk analysis conducted for the business processes and if necessary, are corrective measures applied and registered? | | | |
Purchasing 19. Is feed purchased exclusively from registered or certified suppliers? 20. Is feed purchased exclusively from GMP+ certified suppliers? | | | |
Taking delivery of packaged products in own company premises | | | |
21. Does the company take delivery exclusively of packaged feed that complies with the applicable requirements in order to prevent loss of quality, cross-contamination and/or contamination? (including clean / intact packaging, with label, guarantee date in order) | | | |
Returns 22. Are returns effectively processed? (assessment if return is possible, adequate storage and registration in form 8). | | | |
Storage of packaged products in own company premises 23. Are packaged products stored to ensure preventing loss of quality, cross-contamination and/or contamination? (First In First Out principle to be applied on delivery; do not place feed directly on the ground, separate feed) 24. Are GMP+ assured feed stored separately from non-GMP+ assured feed? Storage of bulk and packaged products by third parties 25. Does the storage company have a valid registration or certification (in the context of FH)? Bulk storage: 26. Does the storage company have a GMP+ certificate? (retain a copy of the certificate in the records, or use GMP+ International database to check validity) Storage of packaged products: 27. Was an agreement signed with the external storage company? See Example agreement (Appendix 2) | | | |
Sales (incl repackaging and delivery) 28. Are products sold exclusively to livestock farms? 29. Are products repackaged? If yes, are the label data of the relevant feed available for inspection? 30. Are additional labeling requirements from TS 1.8 Labelling (for example positive declaration) 31. Are any products sold that are exclusively suitable for a certain species? | | | |
Transport For transport of packaged products in own management 31. Is the load space at all times dry and clean? 32. In the event of combined loads of feed and other products/materials, is cross-contamination prevented? For storage of bulk and packaged products by third parties: 33. Does the carrier have a valid registration or certification (in the context of FH)? Bulk transport by third party: 33. Does the carrier have a GMP+ certificate? (retain a copy of the certificate in the records, or use GMP+ International database to check validity) Transport of packaged products: 34. Was an agreement signed with the external carrier? See Example agreement (Appendix 3) | | | |
35. Are all types of irregularities / deviation situations registered in registration form 8? | | | |
VERIFICATION: In order to check compliance with the requirements in this document, the certified company must verify the system by means of analysis and/or assessment via an internal audit The company may use registration form 4 for conducting such an internal audit.
The verification (internal audit) must be conducted at least once in 12 months. If the answer to any of the questions is “no”, the certified company must take corrective measures and check their effectiveness within one month of their implementation. This working method is to be repeated until full compliance with requirements.
Conclusion: does the feed safety system comply with requirements? If not: which improvements are implemented?
………………………………………………………………………………………………
………………………………………………………………………………………………
REGISTRATION FORM 5: OVERVIEW OF EMPLOYEES
Date: | |||||
Name of employee | Position | Training (add copy of diploma) | Experience (position / years) | Tasks, Responsibilities, Authorisation level | Initial for approval of employee |
| | | | T: R: A: | |
| | | | T: R: A: | |
| | | | T: R: A: | |
| | | | T: R: A: | |
| | | | T: R: A: | |
| | | | T: R: A: | |
REGISTRATION FORM 6: PEST CONTROL
(Frequency: ……………the frequency can be determined based on elements such as hygiene level of spaces)
(add floor plan with numbered places)
NAME OF COMPANY / ORGANISATION IMPLEMENTING PEST CONTROL | ||||||||||||||||||||
NUMBER AND NATURE OF BAIT DISPENSERS | ||||||||||||||||||||
Nature of bait dispenser R /M /FL Þ Date ß | 1 | 2 | 3 | 4 | 5 | 6 | 7 | 8 | 9 | 10 | 11 | 12 | 13 | 14 | 15 | .. | .. | .. | .. | .. |
| | | | | | | | | | | | | | | | | | | | |
| | | | | | | | | | | | | | | | | | | | |
| | | | | | | | | | | | | | | | | | | | |
| | | | | | | | | | | | | | | | | | | | |
| | | | | | | | | | | | | | | | | | | | |
| | | | | | | | | | | | | | | | | | | | |
| | | | | | | | | | | | | | | | | | | | |
| | | | | | | | | | | | | | | | | | | | |
| | | | | | | | | | | | | | | | | | | | |
| | | | | | | | | | | | | | | | | | | | |
O = Taken and refilled (if this was necessary) .
- = Not taken
R = Rat Name of agent / active ingredient………………………………….
M = Mouse Name of agent / active ingredient ………………………………….
FL = Flying pests Name of agent / active ingredient ………………………………….
FINDINGS (RESULTS) BASED ON PREVIOUS TIME …………………………………………………………………………………………………………………………………………………………
COMMENTS AND ACTIONS TAKEN
REGISTRATION FORM 7: CLEANING
(This form must be completed once every 4 months)
Warehouse / point of sale / waste storage (circle applicable option) | |||||
Object | Cleaning method | Name of agent used (if applicable). Please Note: Follow the instructions as stated on the label. | Frequency (daily, weekly, monthly etc.) | Name of responsible person / company / organisation | |
Ceilings | | | | | |
Shelves, racks | | | | | |
Floors | | | | | |
Walls | | | | | |
……… | | | | | |
………. | | | | | |
* Cleaning method: Indicated how this was cleaned: Dry / swept, water / high pressure etc. |
REGISTRATION FORM 8: DEVIATION SITUATIONS
Activity *: | |||
Date | Description of deviation | Improvement measure / solution | Name of employee |
| | | |
| | | |
| | | |
| | | |
| | | |
| | | |
| | | |
| | | |
| | | |
| | | |
| | | |
| | | |
*. Activity: Indicated during which activity the deviation was detected. |
Appendix 1: Recall Plan
The recall plan must include the following elements: The completeness of the plan depends on the organization’s size.
- Reasons for a recall action;
- Responsibilities and authorization of certified company and supplier;
- Responsibilities and authorization of recall coordinator and if applicable, the recall team;
- Criteria for starting and ending the recall;
- Emergency measures;
- Information to own employees;
- Information external: customers, chain links, Certification Bodies, sector organizations, government, media, other stakeholders;
- Example texts of press releases, advertisements, warnings, letters. See below;
- Checklists, lists of contacts, lists of media, lists of external experts;
- Registration of data and experiences;
- Notification and evaluation;
- Aftercare.
Example model recall message (TITLE): “Name of certified company and/or supplier” recalls “product name” “Name of certified company and/or supplier” recalls “product name” with sell-by date “date”. The reason is……….. In order to avoid any risk, we kindly request you to take the relevant article back to (one of the subsidiaries of) “company name”. You will receive your money back when handing in the product. For more information, please feel free to contact: “state Telephone number(s)” We thank you for your cooperation and offer you our apologies for the inconvenience. “company name / company details” |
Appendix 2: Example agreement Storage company
In order to guarantee the safety of the service delivered, storage of packaged products, the storage company (name, address) states that:
- The products are stored and delivered in accordance with the FIFO principle as much possible. Ensure that the date of entry or a lot code is stated on the package if the supplier has not already done this;
- The products are not placed directly on the ground. Instead, pallets or racks are used;
- Feed and non- feed, including crop protection agents, cleaning agents, pest control agents, fertilisers, manure etc. are stored separately in order to prevent cross-contamination
- GMP+ assured feed and non-GMP+ assured feed do not come into contact.
- Visual inspection is regularly conducted on:
- the packaging. The packaging must be clean and intact.
- the guarantee date The product is not past its guarantee date.
- In the event of non-compliance with the above-mentioned quality aspects, the certified company (name certified company) is notified of this as soon as possible;
- ………. (the certified company may decide on supplementary conditions).
Place and date : …………………………..
Signature : …………………………..
Appendix 3: Example agreement Transport company
In order to guarantee the safety of the service delivered, the carrier (name, address) states that, before the load space is used for transporting packaged products:
- The loading compartment is clean and dry;
- The load space is completely empty and free of load residue and smell of previous loads;
- A suitable cleaning regime is carried out if the load space should not comply with the requirements under a and b. The load space must at least be swept.
- cross-contamination is prevented in the event of combined loads of feed and other products/materials;
- In the event of non-compliance with the above-mentioned quality aspects, the certified company (name certified company) is notified of this as soon as possible;
- ………. (the certified company may decide on supplementary conditions).
Place and date : …………………………..
Signature : …………………………..
Feed Support Products
That was a lot of information to digest and one might ask, what is the next step? Luckily we can offer support for the GMP+ Community when doing this. We provide support by means of various tools and guidances but as each company has a shared responsibility to feed safety, and therefor tailor-made solutions cannot be offered. However, we do help by explaining requirements and provide background information about the requirements.
We have developed various supporting materials for the GMP+ Community. These include various tools, ranging from Frequently Asked Questions (FAQ) lists to webinars and events.
Supporting materials related to this document (Guidelines and FAQ’s)
We have made documents available which give guidance to the GMP+ requirements as laid down in the module GMP+ FSA and GMP+ FRA. These documents give examples, answers to frequently asked questions or background information.
Find our Feed Support Products here: Guidelines More information: https://www.gmpplus.org/feed-certification-scheme/scheme-documents/support/ |